啤小奕™AI助手:用智慧基因重塑啤酒产业未来
在全球啤酒产业竞争日益激烈的今天,数字化转型已成为企业降本增效、提升核心竞争力的必由之路。灵奕集团凭借对工业智能化的深刻洞察,推出全球首款深度融合大模型与RAG技术的啤小奕™AI助手,为啤酒生产全流程注入智慧基因,助力企业实现从知识管理到智能决策的全面升级。
一、大模型+RAG双擎驱动
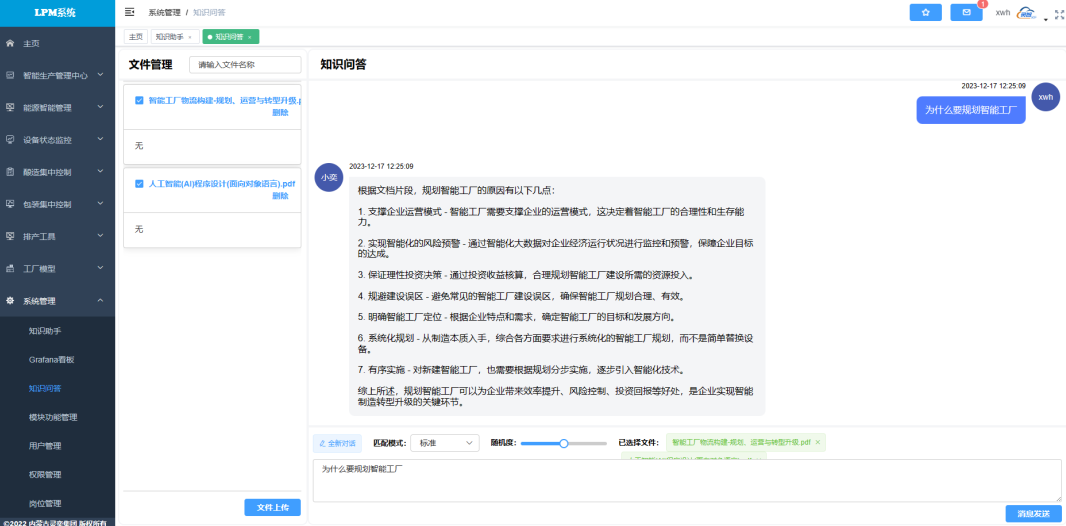
在工业场景中,传统AI往往受限于知识的碎片化与决策的滞后性。啤小奕™AI助手通过三大核心技术突破,构建起啤酒产业的智能中枢:
01
双引擎深度耦合

基于百亿参数工业大模型,结合实时检索增强生成技术(RAG),啤小奕™实现了对啤酒生产知识的精准理解与动态扩展。通过自研的跨文档语义检索算法,可在0.3秒内完成工艺手册、设备日志、质检报告等千份文档的关联分析,确保回答准确率高达98.6%。例如当发酵罐温度异常时,系统不仅调取SOP规程,还能自动关联历史维修记录与环境参数波动数据,提供多维度的处置建议。
02
多模态工业知识图谱

构建覆盖原料、工艺、设备、质量四大领域的动态知识网络,将文本、图像、时序数据深度融合。每个麦芽检测指标背后关联着供应商档案、历年质检波动曲线;每台糖化设备的振动频谱图实时映射到故障知识库。这种立体化知识表达使新员工通过自然语言提问即可获取结构化专家经验。
03
边缘-云端协同计算架构

采用分布式计算框架,在本地部署轻量化推理引擎保障实时响应,同时通过云端持续训练模型。当某工厂发现新型设备故障代码时,知识库可72小时内完成全国产线的同步更新,形成"单点突破-全局共享"的智慧进化闭环。

二、四大核心模块重构生产价值链
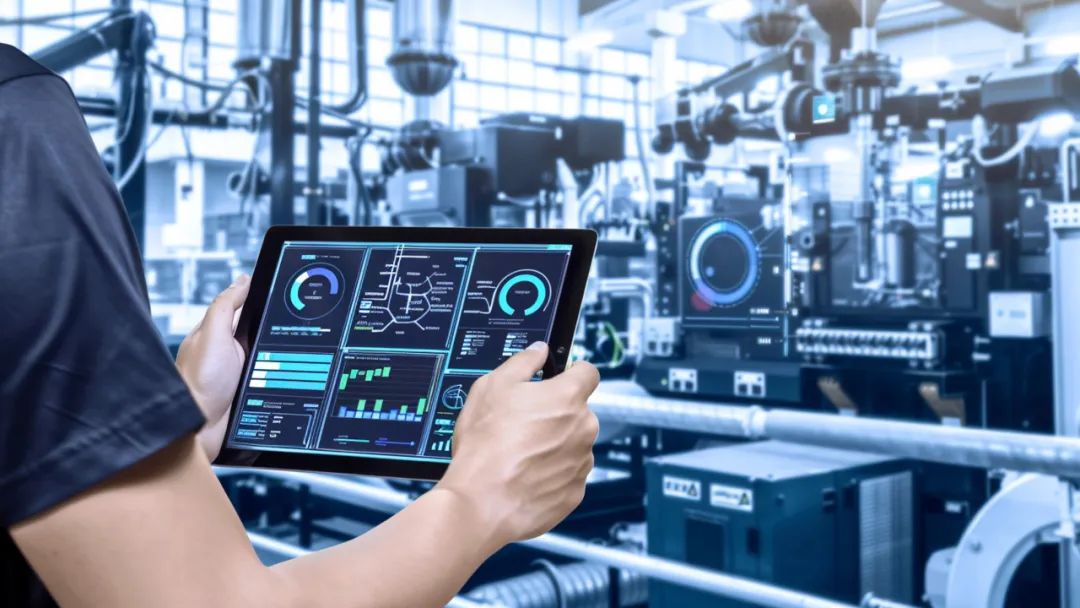
啤小奕™AI助手并非孤立工具,而是贯穿“知识-执行-决策”全链路的智能操作系统:
01
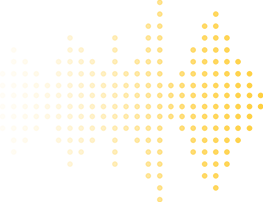
企业知识中枢(EKS)
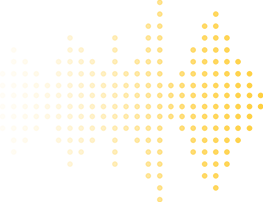
1
秒级构建数字工艺图书馆:自动解析PDF、CAD图纸等非结构化文档,智能标注300+关键控制点;
2
动态关联MES生产数据:将工艺参数与实时产量、能耗数据可视化对照;
3
智能问答工作台:支持"糖化碘值异常的可能原因排序"等复杂问题多轮追问。
02
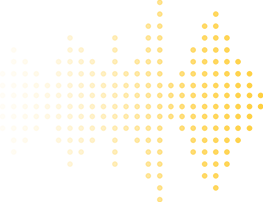
工艺智控平台
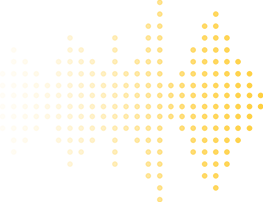
1
设备健康度监控:实时监测12类关键设备运行状态,自动生成设备健康度画像;
2
异常预测系统:基于LIMS检测数据的预警模型,提前4小时预测发酵异常概率;
3
参数优化模拟器:输入麦芽批次特性,智能推荐糖化温度曲线。
03
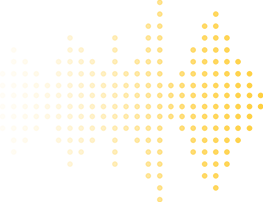
人才赋能体系
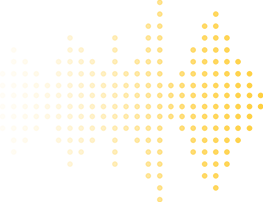
1
AR辅助巡检:扫描设备二维码即可调取3D拆解动画与操作禁忌;
2
专家经验数字化:通过对话式交互萃取老技师隐性知识,构建可传承的故障处置决策树;
3
智能培训系统:根据岗位自动生成学习路径,新员工上岗周期缩短67%。
04
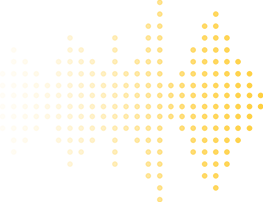
智能决策引擎
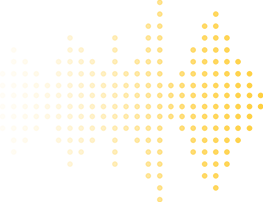
1
异常处置知识图谱:当灌装线突发停机时,自动匹配近三年相似案例的处置时效与成本;
2
工艺改良推演系统:输入目标酒精度与成本约束,输出多套参数优化方案及风险预测;
3
供应链智能调度:结合原料库存、设备产能、物流数据生成最优排产计划。

三、客户应用
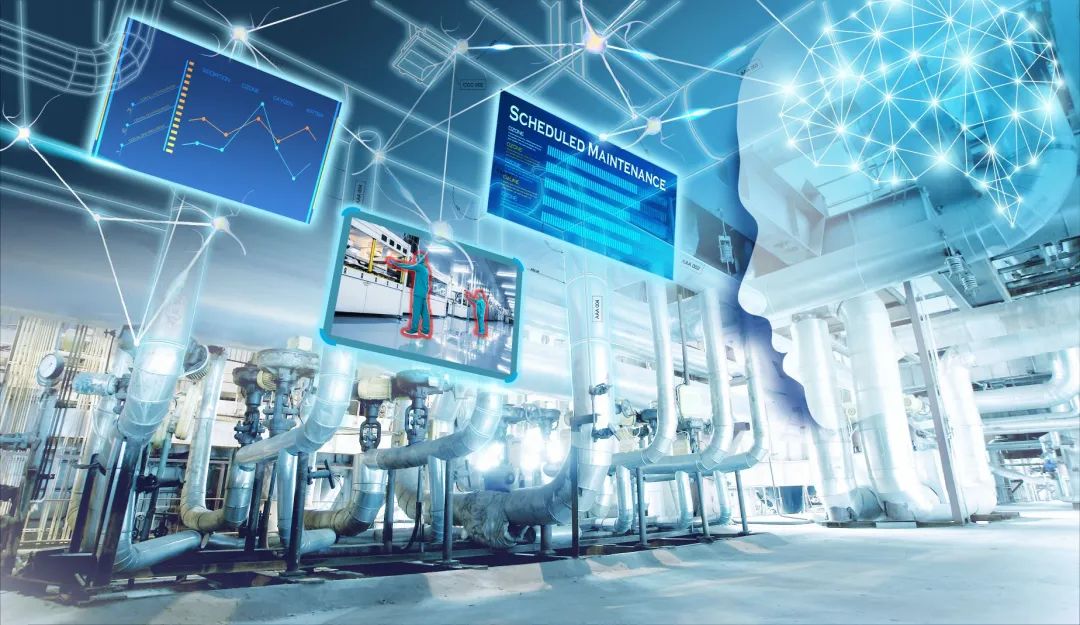
在20余家头部啤酒企业的实践中,啤小奕™已形成可复制的智能化升级范式:
场景1:质量异常秒级溯源
某厂商发现某批次啤酒浊度超标,传统排查需跨部门协同3天。通过啤小奕™输入"浊度异常+生产日期",系统即刻关联:
-
当日洗瓶机压力波动记录
-
同批次酵母活性检测曲线
-
追溯该生产批次对应的原料粉碎度,过滤曲线等数据。
最终锁定洗瓶机喷嘴堵塞问题,处理时效提升85%。
场景2:工艺参数全局优化
在开发低醇啤酒过程中,工程师提出"如何在保证风味前提下降低发酵度"的命题。啤小奕™立即完成:
-
调取全球180篇相关专利的核心参数区间
-
比对近三年车间温控数据与风味评价关联模型
-
生成3套优化方案并模拟预测酒精度波动范围
最终将研发周期从6个月压缩至45天。
场景3:设备预测性维护
通过分析离心泵振动频谱与故障代码的时空相关性,啤小奕™成功预测某产线设备轴承磨损趋势,在计划性检修前72小时推送更换建议,避免非计划停机。

结语:开启啤酒产业的认知革命

在数字经济与实体经济深度融合的今天,啤小奕™AI助手正在重新定义啤酒生产的可能性。它不仅是知识管理系统,更是企业核心竞争力的放大器——通过将人类经验转化为可计算、可进化、可传承的智能资产,助力啤酒企业在品质控制、工艺创新、人才培养等维度构建全新护城河。灵奕集团将持续深耕工业智能赛道,让每一滴啤酒都闪耀智慧的光芒。
联系电话
0471-6925106
商务邮箱
sales@lingyi.group
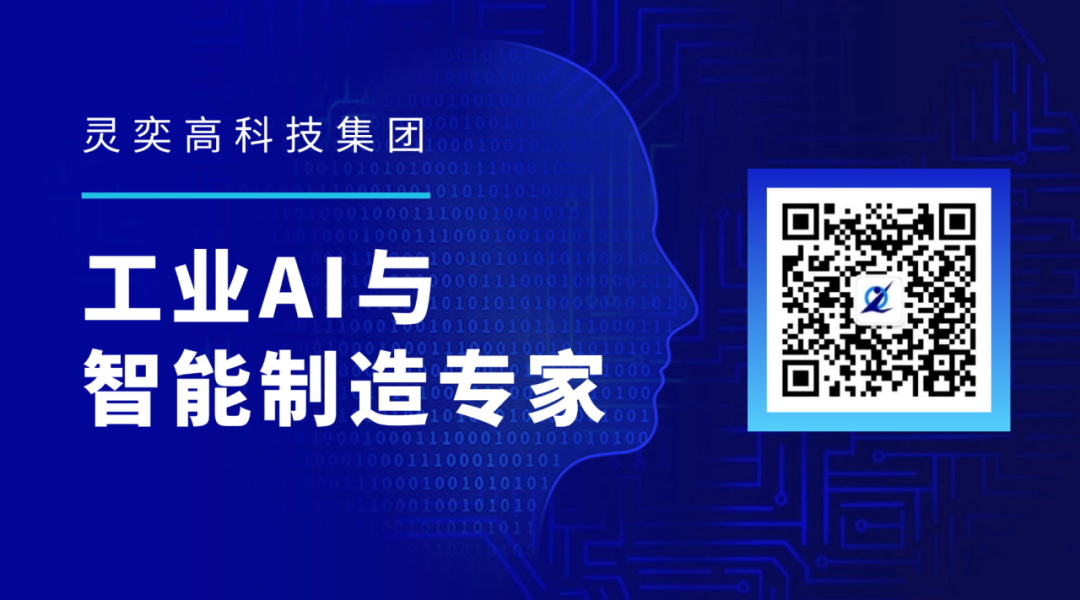